ABOUT
Earl Terminal was born out of necessity. What was that necessity, you ask ? There was a need to maximize the performance of electronic components which comprise car audio sound systems.
It turns out that the same challenges that plagued the car audio industry shared common ground with other categories of automotive and consumer electronics. Equipment performance, regardless of category, name brand or reputation relies primarily on one key factor: flow of electricity, also known as electrical continuity.
Most people do not realize DC (Direct Current) electricity (used in automobiles) actually flows from negative to positive – not the other way around. What this means is that ground connections are more important than the power connections. This fact was either omitted or neglected in every day practical application for decades !
To make matters worse, the integrity of ground connectivity has often been the single most significant weakness in car audio sound system and vehicle electronics installation. Innovation was needed to solve this common ground (pun intended) that plagued all aftermarket component installers.
Innovators create solutions, but don’t often implement them. Creation of solutions is not enough. Problems must be addressed. Okay, that’s obvious; however, history has proven that a majority of installation professionals simply learned to cope with ground problems, nothing more. Other professionals weren’t even aware that there was a problem. In either case, coping does not elicit change, much less lead to effective solutions.
Ironically, problem solvers don’t cope well with problems! Problem solvers are driven to make problems vanish and resolutions appear. Problem solvers are different from innovators in one key aspect: They take action !
Well guess what, taking action is still not enough ! The action taken must yield real results which eliminate problems – long term. Results do not come easily. Achieving results requires the sweat equity of people who never give up, who never compromise, and who never settle for a “repainted status quo”.
These people are Achievers ! Achievers are uncommon in society, much less in industry.
Earl A Lirrette III is one of those rare and special individual who just doesn’t settle for mediocrity. For Earl, there are only two choices: achieving excellence and striving toward better excellence. His success oriented mindset was formed over 38 years ago.
In February of 1984, when Earl was in the 11th grade, he started working as a car stereo installer at a shop named Apple Audio located in Louisiana. As Earl began to hone his craft, he discovered the reoccurring problem of grounds coming loose on installations.
Through various trials and remedies evolved a simple solution of overlocking the hardware so it would not loosen just as a carpenter toe nails lumber.
After approximately 10 years of the trials at the shop now known as Tiger Audio, the patent was filed in November of 2011. Thus, Earl Terminal was born. Cumulatively speaking, even real car people, do not realize that in a DC electrical system, electricity actually flows from negative to positive. Not the other way around.
Therefore, in 12-volt chassis ground vehicles, this makes the ground connection even more important than the power connection.
Secondly, in regards to a mobile audio system, if a weak ground exists on one unit versus another, there is a potential voltage difference between the two or more units. When this happens, typically the audio signal can be degraded, or, in many cases, noise can enter the system through a “ground loop”.
In extreme cases, when grounds fail catastrophically, the components will attempt to keep themselves grounded by seeking a ground path through the signal cables that connect them to each other. Typically, in car audio applications, these are the RCA style signal wires. When that happens, extreme amounts of current can flow to where it doesn’t belong, destroying the output sections of radios, the input sections and sometimes, the power supply sections of amplifiers.
Most recently, with more and more computer based systems in vehicles that rely on data transfer to different electrical components, a bad ground can cause any number of odd results. “Data” in the vehicle automotive space is usually just a measurement of voltage to ground, so, if you start off with a weak connection to ground, chances are good that your data won’t transfer correctly and confuse a different component down the line, or, worse yet, won’t be received at all.
So that explains the main reasons you want, no, NEED a good ground.
What usually happens in car audio is that the ground wire of a component is crimped onto a ring terminal.
This type of connector is great for battery posts, but, when it comes to a ground, you want to secure a ground that is as close as possible to the component for optimal current flow, making sure that it’s the best ground possible along with wire costs savings. In order to accomplish this, installers usually scrape paint off the nearest area of sheet metal and use a sheet metal screw to affix the ring to the car. These types of terminals have an inherent design flaw. Since they have one attachment point, they can easily loosen and rotate over time, which will lead to ground failure and lost performance in automotive electrical systems.
One point to mention, automobiles are nominally 12-volt systems, so, when you lose one volt to a bad connection, that’s nearly 10% of the available power that you have. Ten percent is HUGE ! Also, as the connection degrades, extra heat will be generated and the problem will only get worse.
A ring terminal looks like this:
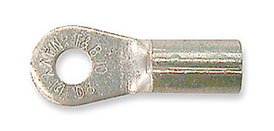
Installers, being innovators by nature, have solved this by the following example (in the middle, below) and, in an attempt of overkill, the bottom image.
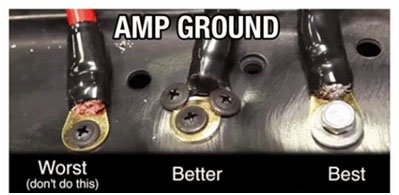
Note the one labeled “best” can still rotate……
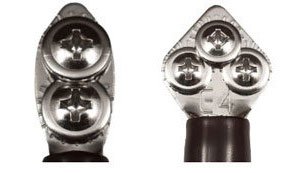
You can see that from the example below, the screw holes are aligned in the terminals in a very methodical way. When using appropriate screws, the second (and depending upon terminal size, third) screws overlock the main attachment screw, assuring that the main screw can NEVER come loose. Also, more surface area is allotted to the terminal, since more surface area equals better contact area. The more contact area, the more electrons can flow into the wire with less resistance.
Furthermore, there are serrations both in the ferrule area of the terminal (that’s the part you crimp to the wire) to ensure the terminal grabs the wire and holds it securely. There’s also serrations around the screw holes that help the screws stay tight.
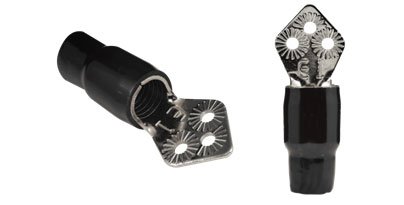
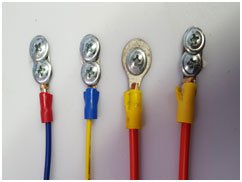
From this perspective, you can see the overlocking screw in action, and see how the camber of the overlocking screw also serves to bind the screws to the sheet metal.
The end result is literally the ring terminal re-imagined, using 58 years plus of combined experience in the field seeing what problems arise and what the root cause is.
It’s almost ALWAYS the ground !
ABOUT
Earl Terminal was born out of necessity. What was that necessity, you ask ? There was a need to maximize the performance of electronic components which comprise car audio sound systems.
It turns out that the same challenges that plagued the car audio industry shared common ground with other categories of automotive and consumer electronics. Equipment performance, regardless of category, name brand or reputation relies primarily on one key factor: flow of electricity, also known as electrical continuity.
Most people do not realize DC (Direct Current) electricity (used in automobiles) actually flows from negative to positive – not the other way around. What this means is that ground connections are more important than the power connections. This fact was either omitted or neglected in every day practical application for decades !
To make matters worse, the integrity of ground connectivity has often been the single most significant weakness in car audio sound system and vehicle electronics installation. Innovation was needed to solve this common ground (pun intended) that plagued all aftermarket component installers.
Innovators create solutions, but don’t often implement them. Creation of solutions is not enough. Problems must be addressed. Okay, that’s obvious; however, history has proven that a majority of installation professionals simply learned to cope with ground problems, nothing more. Other professionals weren’t even aware that there was a problem. In either case, coping does not elicit change, much less lead to effective solutions.
Ironically, problem solvers don’t cope well with problems! Problem solvers are driven to make problems vanish and resolutions appear. Problem solvers are different from innovators in one key aspect: They take action !
Well guess what, taking action is still not enough ! The action taken must yield real results which eliminate problems – long term. Results do not come easily. Achieving results requires the sweat equity of people who never give up, who never compromise, and who never settle for a “repainted status quo”.
These people are Achievers ! Achievers are uncommon in society, much less in industry.
Earl A Lirrette III is one of those rare and special individual who just doesn’t settle for mediocrity. For Earl, there are only two choices: achieving excellence and striving toward better excellence. His success oriented mindset was formed over 38 years ago.
In February of 1984, when Earl was in the 11th grade, he started working as a car stereo installer at a shop named Apple Audio located in Louisiana. As Earl began to hone his craft, he discovered the reoccurring problem of grounds coming loose on installations.
Through various trials and remedies evolved a simple solution of overlocking the hardware so it would not loosen just as a carpenter toe nails lumber.
After approximately 10 years of the trials at the shop now known as Tiger Audio, the patent was filed in November of 2011. Thus, Earl Terminal was born. Cumulatively speaking, even real car people, do not realize that in a DC electrical system, electricity actually flows from negative to positive. Not the other way around.
Therefore, in 12-volt chassis ground vehicles, this makes the ground connection even more important than the power connection.
Secondly, in regards to a mobile audio system, if a weak ground exists on one unit versus another, there is a potential voltage difference between the two or more units. When this happens, typically the audio signal can be degraded, or, in many cases, noise can enter the system through a “ground loop”.
In extreme cases, when grounds fail catastrophically, the components will attempt to keep themselves grounded by seeking a ground path through the signal cables that connect them to each other. Typically, in car audio applications, these are the RCA style signal wires. When that happens, extreme amounts of current can flow to where it doesn’t belong, destroying the output sections of radios, the input sections and sometimes, the power supply sections of amplifiers.
Most recently, with more and more computer based systems in vehicles that rely on data transfer to different electrical components, a bad ground can cause any number of odd results. “Data” in the vehicle automotive space is usually just a measurement of voltage to ground, so, if you start off with a weak connection to ground, chances are good that your data won’t transfer correctly and confuse a different component down the line, or, worse yet, won’t be received at all.
So that explains the main reasons you want, no, NEED a good ground.
What usually happens in car audio is that the ground wire of a component is crimped onto a ring terminal.
This type of connector is great for battery posts, but, when it comes to a ground, you want to secure a ground that is as close as possible to the component for optimal current flow, making sure that it’s the best ground possible along with wire costs savings. In order to accomplish this, installers usually scrape paint off the nearest area of sheet metal and use a sheet metal screw to affix the ring to the car. These types of terminals have an inherent design flaw. Since they have one attachment point, they can easily loosen and rotate over time, which will lead to ground failure and lost performance in automotive electrical systems.
One point to mention, automobiles are nominally 12-volt systems, so, when you lose one volt to a bad connection, that’s nearly 10% of the available power that you have. Ten percent is HUGE ! Also, as the connection degrades, extra heat will be generated and the problem will only get worse.
A ring terminal looks like this:
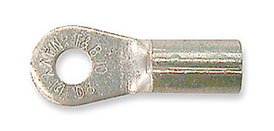
Installers, being innovators by nature, have solved this by the following example (in the middle, below) and, in an attempt of overkill, the bottom image.
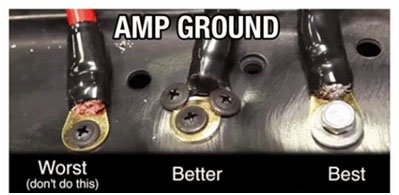
Note the one labeled “best” can still rotate……
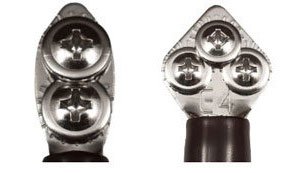
You can see that from the example below, the screw holes are aligned in the terminals in a very methodical way. When using appropriate screws, the second (and depending upon terminal size, third) screws overlock the main attachment screw, assuring that the main screw can NEVER come loose. Also, more surface area is allotted to the terminal, since more surface area equals better contact area. The more contact area, the more electrons can flow into the wire with less resistance.
Furthermore, there are serrations both in the ferrule area of the terminal (that’s the part you crimp to the wire) to ensure the terminal grabs the wire and holds it securely. There’s also serrations around the screw holes that help the screws stay tight.
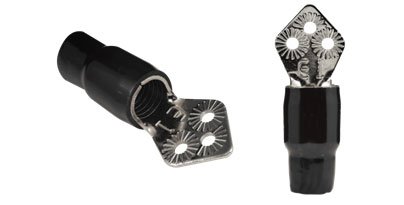
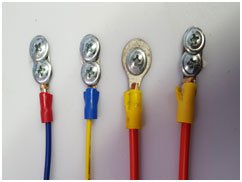
From this perspective, you can see the overlocking screw in action, and see how the camber of the overlocking screw also serves to bind the screws to the sheet metal.
The end result is literally the ring terminal re-imagined, using 58 years plus of combined experience in the field seeing what problems arise and what the root cause is.